「建設業での資材の在庫管理は、どうやれば上手くいく?」
「在庫管理でミスが多くて困っている。やり直したいけど、どこから手をつけていいかわからない…」
建設業では同時進行するプロジェクトごとに扱う資材の種類や数量が大きく変動するため、正確に資材の在庫数を把握するのは簡単ではありませんよね。
建設業の方が資材の在庫管理をスムーズに行うには、以下の5つのステップで進めるのがおすすめです。
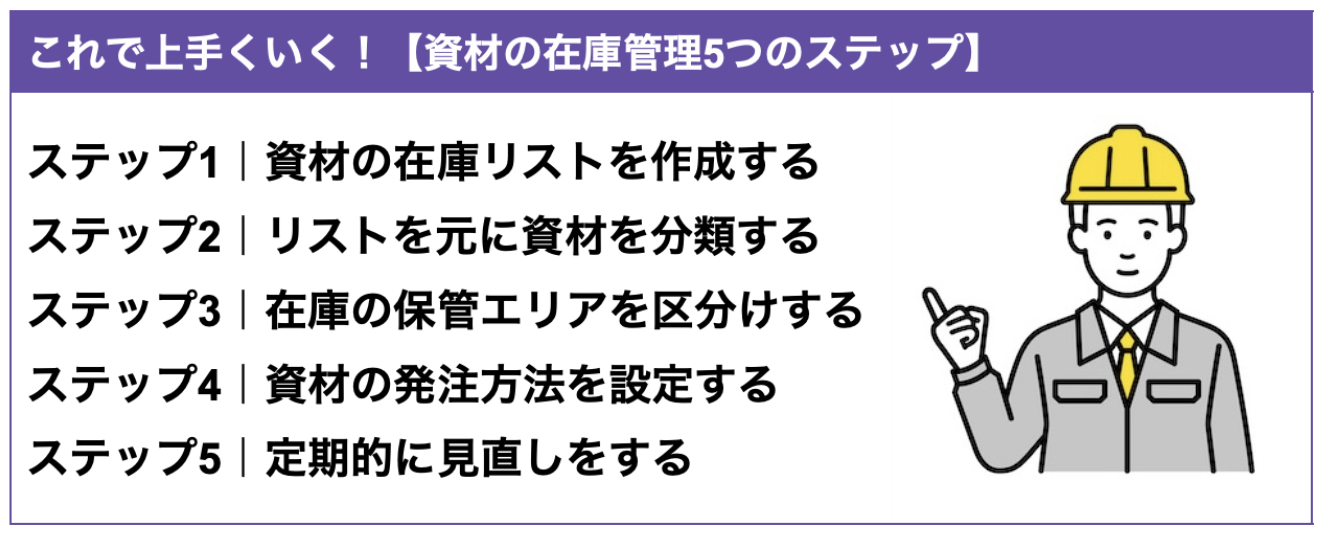
まずはじめに、今ある資材の全てをしっかりとリストにまとめて、全体像を把握することが重要です。
なぜなら、資材の全体像をリスト化することで、効率的な在庫管理を実現するための土台を作ることができるからです。
基本的なことではありますが、このリスト作成が後の在庫管理効率を大幅に高める鍵となりますので、面倒くさがらずに、一気に行ってしまいましょう。
この記事では、各ステップで在庫の整理や適切な在庫管理を効率的に行う方法を具体的にご紹介していきます。
記事に沿って進めれば、現在抱えている在庫管理の課題がスッキリ解消し、業務負担の軽減・コスト削減を実現できるでしょう。
ぜひ、最後まで目を通していただけたらと思います。
1.【一覧】建設業|資材の在庫管理の流れ
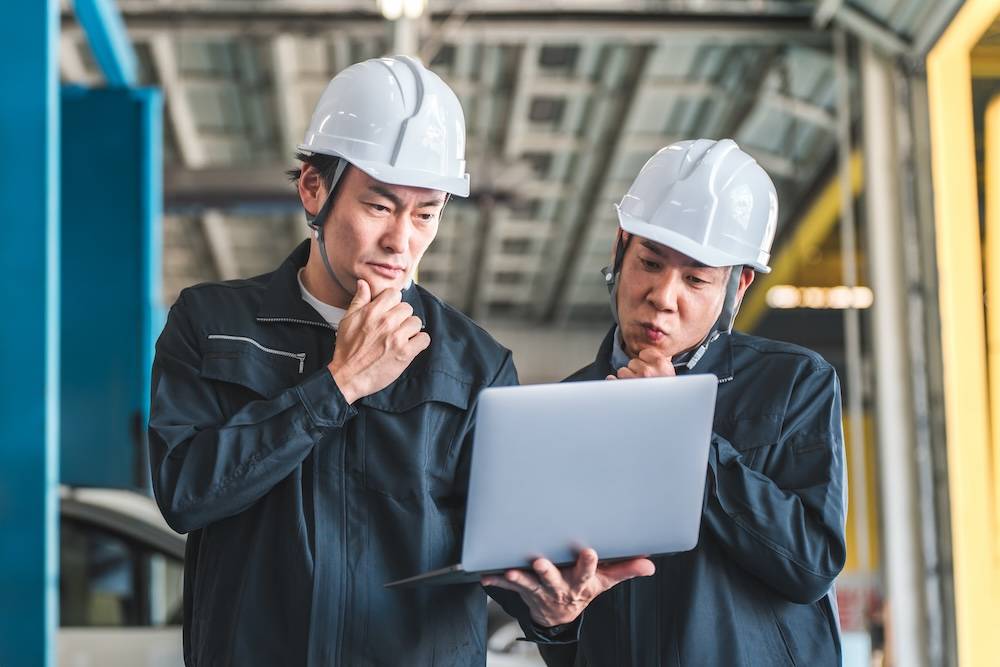
建設業での、資材の在庫管理はプロジェクトの進行を円滑にする上で欠かせない重要なプロセスです。
まず1章では、適切な資材の在庫管理業務の全体の流れを把握しましょう。
各ステップと概要を示した下表をご覧ください。
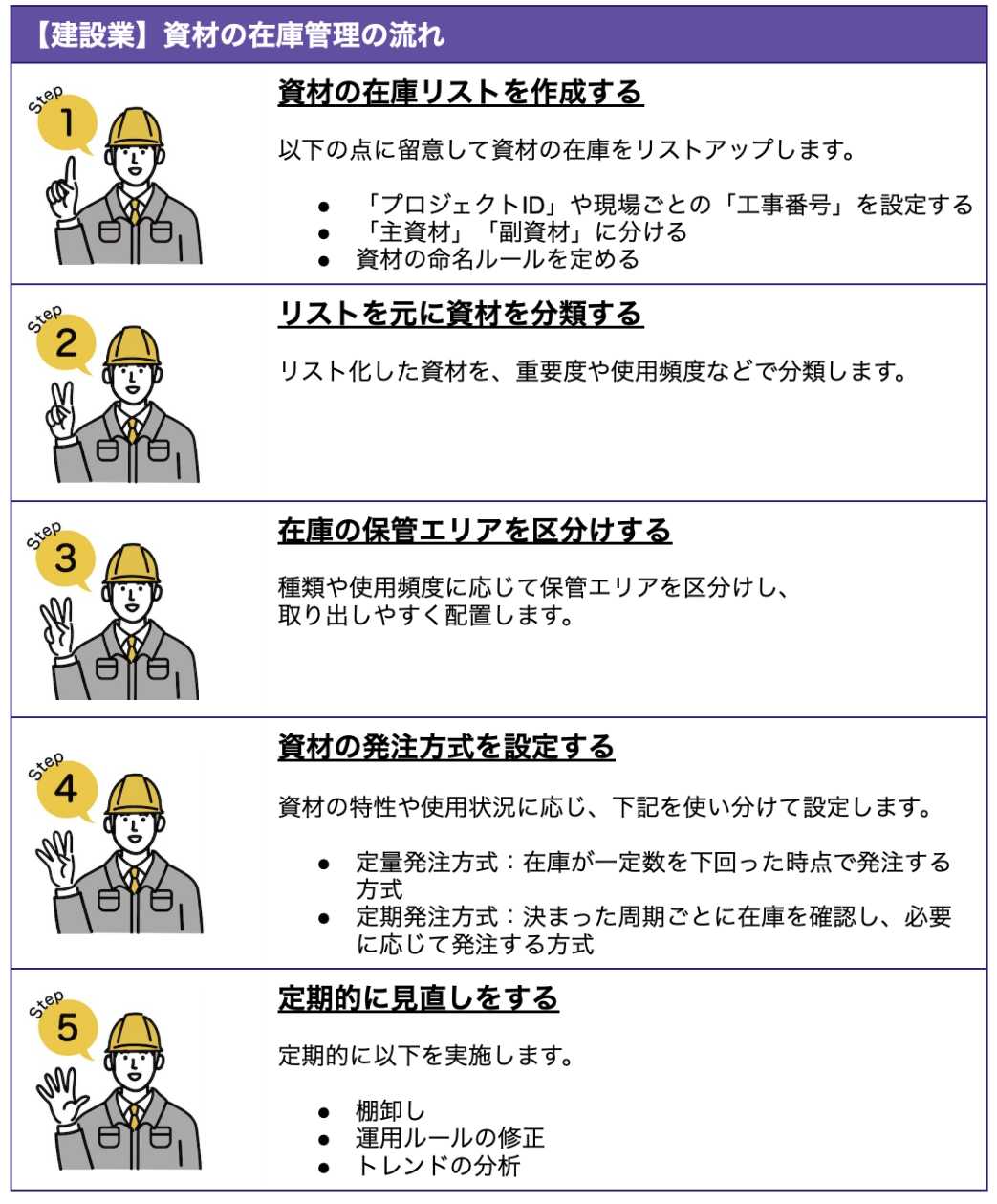
資材の在庫管理は、このようなステップで行います。
次章からは、それぞれの内容を詳しく解説しますので、順を追ってみていきましょう。
2. ステップ1:【重要】資材の在庫リストを作成する
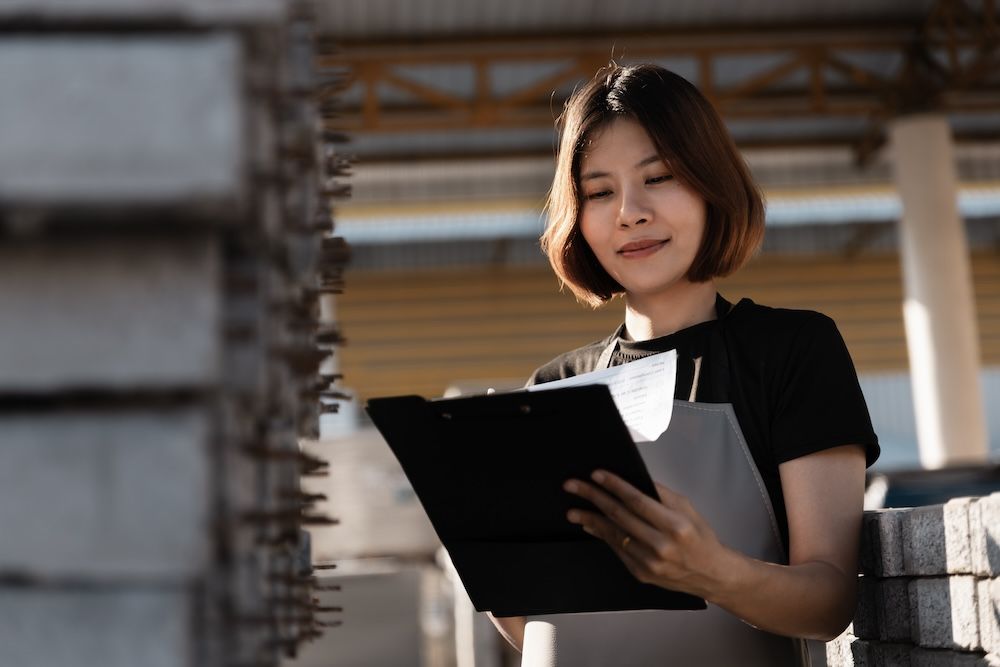
最初のステップは、今ある資材の在庫のリストアップです。
冒頭でもお伝えしましたが、ここのステップの精度が、今後の資材の在庫管理の精度を左右すると言っても過言ではありません。
現在の在庫管理帳簿が、プロジェクトごとや、事業所ごとなど複数に分かれている場合は、1つのフォーマットに統一しましょう。そして、主資材だけでなく副資材も含めて全てをここでリストアップすることが重要です。
この章では、リストアップの際に留意すべきポイントを踏まえてリストの作成方法を解説します。
- 「プロジェクトID」や現場ごとの「工事番号」を設定する
- 「主資材」「副資材」に分ける
- 資材の命名ルールを定める
この章の最後に、ダウンロードして使える在庫管理のテンプレートをご用意しましたので、そちらを使用してリストを作成してみましょう。
リストアップを丁寧に行うことで、後々の管理が格段にスムーズになりますよ。
しっかりポイントを把握して、管理しやすいリストを作成しましょう。
2-1.「プロジェクトID」や現場ごとの「工事番号」を設定する
まずリストに記載すべき項目として、「プロジェクトID」や現場ごとの「工事番号」を設定しましょう。
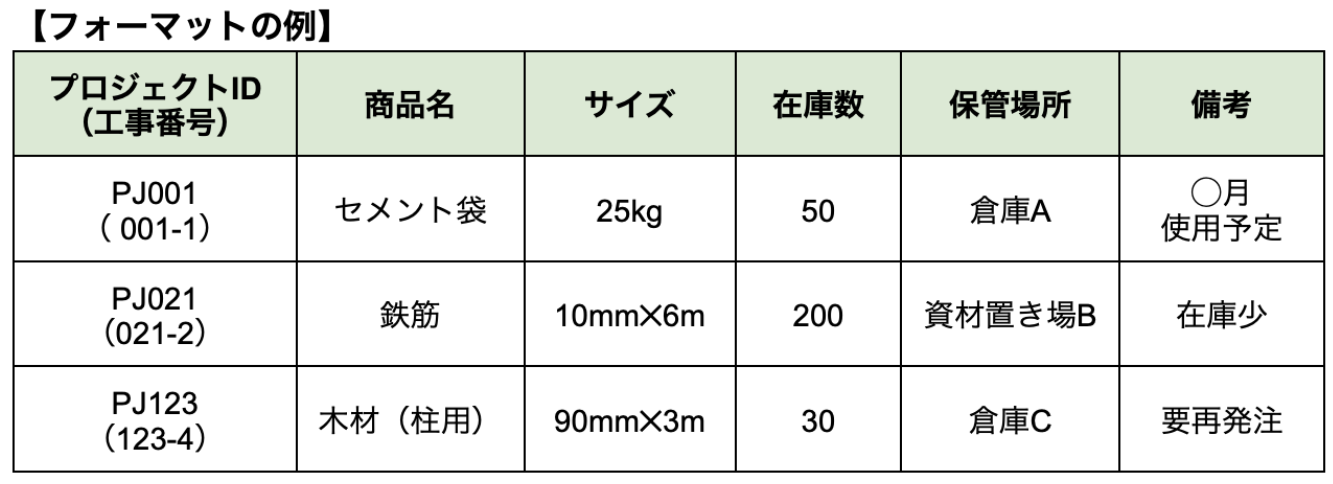
リストにプロジェクトIDも含めて管理することで、資材がどの現場に所属するかが明確になり、混同を防ぐことができます。
特に、複数のプロジェクトが同じ現場内で進行している場合、この設定が重要です。
たとえば、現場Aに複数のプロジェクトが存在している場合、それぞれに異なる「プロジェクトID」と「工事番号」を割り当てます。
記載例 |
---|
【現場A】 プロジェクトID: PJ001(工事番号: 001) プロジェクトID: PJ002(工事番号: 002) プロジェクトID: PJ003(工事番号: 003) 【現場B】 |
さらに、特定の工事区分を示す場合には、「工事番号」を 001-1, 001-2 のように細かく分けることで、管理の精度を高めることもできます。
IDや番号を設定することで、どの資材がどのプロジェクトや工事区分に使われるべきかの割り当てを間違えたり、混乱したりすることを防ぎ、適切な管理をすることができます。
2-2.「主資材」だけでなく「副資材」もリストに記載する
リスト作成時には、鉄骨や木材などの「主資材」だけでなく、ボルトや接着剤といった「副資材」も漏れなく記載しましょう。
消耗品も含まれる副資材は、主資材に比べて不足しやすいため、事前の管理や確認が重要です。
主資材建物や構造物の主要部分を作るために使う重要な資材。 プロジェクトにとって必須であり、進行に直接的な影響を与える資材で、建物の骨組みや基礎部分を作るための鉄骨や木材、コンクリートなどがこれに当たります。 例)鉄骨、木材、コンクリート、ガラスなど |
副資材主資材を補助する役割を果たすもので、施工を円滑に進めるために必要な資材。 必須ではないものの、在庫状況が工事の品質や進捗に重要な影響を与える場合があります。 例)接着剤、ボルト、電線、ペンキ、消耗品(マスク、手袋、工具)など |
工事の主要部分を構成する「主資材」に比べ、目立たない存在の「副資材」ですが、工事の完成度やスムーズな進行において欠かせない役割を果たします。
副資材の何かが不足しただけで、作業の進捗が遅れ、全体の品質に影響を与える可能性があります。
「副資材」も含めた、資材の適切なリスト化を徹底しましょう。
2-3. 資材の命名ルールを定める
リストに記載する際の、資材の命名ルールを定めましょう。
ルールを定めることで、リストが視覚的に整理され、後の管理が容易になります。
具体的には、以下の要素について記載ルールを設定しましょう。
- 商品コード
- 商品名
- カテゴリ
- サイズ
【記載の参考例】
【商品コード】資材ごとのアルファベットや番号を設定します。 例:STL-001(スチール材-番号1) |
【商品名】簡潔で内容が分かりやすい名前を付けます。 例:鉄筋25mm、電線10mm |
【カテゴリ】資材を管理しやすいように分類します。 例:金属、木材、工具 |
【サイズ】資材の寸法(必要な場合は重量)を、統一されたフォーマットで記載します。 例:25mm x 6000mm |
ルールを定めて記載することで、リストは一目で理解しやすく、後の検索や更新も容易になります。
リスト作成は在庫管理の基盤です。
分かりやすく正確なリストを目指しましょう。
※下記をダウンロードし、コピーして使用してください。項目は貴社の必要に応じて自由に変更できます。
在庫管理テンプレート
3. ステップ2:リストを元に資材を分類する
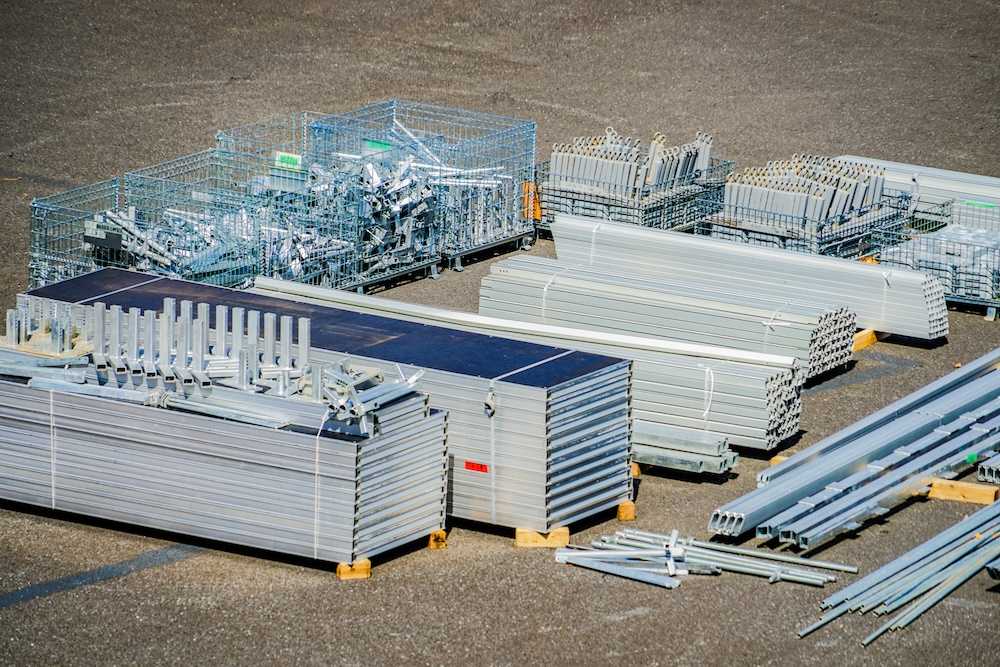
次のステップは、資材の分類です。
リスト化した資材を、重要度や使用頻度などで分類します。
分類方法はさまざまありますが、ここでは一般的によく用いられる「ABC分析」をベースにした分類方法をご紹介します。
※ABC分析:使用頻度やコストに応じて在庫品を以下のようにランク分けする方法
- ABC分析で分類する
- ABC分析と他の分類基準を組み合わせる
まずABC分析で分類し、それと、自社に便利な他の分類基準とを組み合せることで在庫管理が効率的に行えます。
それぞれ解説しますので、しっかり理解して取り入れていきましょう。
3-1. ABC分析で分類する
ABC分析とは、使用頻度やコストなどの指標を大きい順にABCの3つにランク付けし、優先度を決めて管理していく手法です。
まず、リストに載っている資材各々について「どれくらいの頻度で使うか」、「コストはどれくらいか」を考えます。たとえば、
- 鉄骨は建設の初期段階でたくさん使うのでAランク
- 塗料は、現場によって異なりますが、頻繁に使うならBランク
- クリップはほとんど使わないのでCランク
というように分類します。
わかりやすく示した下表をご覧ください。
ABC分析を使った資材の分類(例) |
---|
Aランク(使用頻度が高くコストも高い) |
例:鉄骨、木材 鉄骨や木材は建設に欠かせない材料で、よく使用されます。 |
Bランク(使用頻度はそれほど高くないが重要な資材) |
例:配管材、塗料 特定の配管材や塗料は、頻繁には使いませんが、現場によっては必要な時があります。 |
Cランク(使用頻度が低くコストが比較的低い) |
例:接着剤、クリップ 接着剤やクリップは少しだけ使うものなので、在庫量は少なくても問題ありません。 |
分類が終わったら、それぞれのランクに適した管理方法を考えましょう。
3-2. ABC分析と他の分類基準を組み合わせる
ABC分析だけでは現場や企業の具体的なニーズに十分対応できない場合があります。
そこで、ABC分析に加えて、自社に適した分類基準を組み合わせることで、より柔軟で実用的な資材管理が可能になります。
以下に、ABC分析と相性の良い分類の基準をいくつかご紹介します。
これらの1つ、または複数を取り入れることで、在庫管理の精度を高めることができますので、ご覧ください。
ABC分析と組み合せると良い分類の基準(例) |
---|
1.ABC分析+【プロジェクト】別分類ABC分析でランク分けした資材を、さらに各プロジェクトごとのリストに基づいて分類します。 各プロジェクトで必要な資材をセットとして管理することで、混同を防ぎます。 おすすめのケース:特に複数のプロジェクトが並行して進行している場合に効果的です。 |
2.ABC分析+【消耗期限・耐久性】別分類 消耗期限や耐久性の観点から、「短期保管」「長期保管」というような形で分類します。 腐食しやすい金属資材や劣化する化学製品(例: セメントや接着剤)を優先的に使うことで、無駄や損失を削減できます。 おすすめのケース:消耗期限が短い、あるいは、特定の環境で保存状態に影響を受けやすい資材を管理する場合に有効です。 |
3.ABC分析+【サイズ・重量】別分類 ABC分析した資材に対して、「軽量・小型」「中型」「大型・重量物」といった分類を加えます。 大型資材は地面に近い場所、小型資材は棚上部に保管するなど、効率的な倉庫レイアウトの設計に役立ちます。 おすすめのケース:保管場所に制約がある場合や、効率的なスペース利用を重視する場合に効果的です。 |
これらの基準をプロジェクトや資材の特性に応じてABC分析と組み合わせると、資材管理の精度がさらに向上します。
運用や保管の観点も加わることで、より実用的な管理が可能になります。
チェック!在庫回転率を確認しておきましょう |
---|
このステップの際に、主資材・副資材ごとに、資材がどのくらいのペースで消費されるかを確認して、在庫回転率を把握しておくと良いでしょう。在庫回転率は、一定期間にどれだけの在庫が消化されたかを示す指標で、以下の計算式で求められます。 在庫回転率 = 売上原価(または消費した資材の総額) ÷ 平均在庫額 この計算によって、在庫がどれだけ効率的に消費されているかが把握できます。
在庫回転率を把握しておくと、補充のタイミングを適切に見極められるため、無駄な在庫や欠品のリスクが軽減できます。 |
4. ステップ3:在庫の保管エリアを区分けする
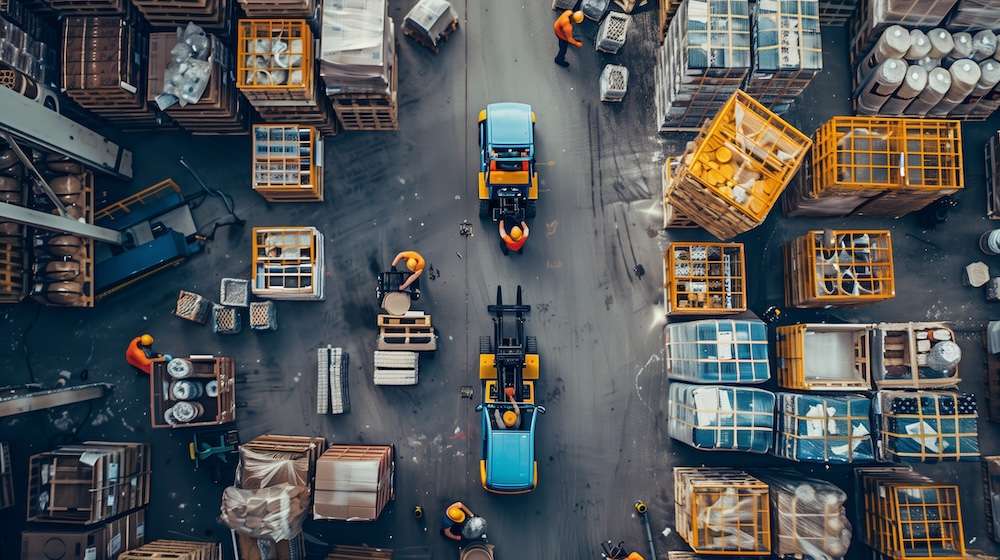
分類ができたら、資材の種類や使用頻度に応じて保管エリアを区分けし、取り出しやすく配置します。
取り出しやすい配置の決め方は各社の事情により違ってきますが、基本的には次のようなプロセスで行うと良いでしょう。
- 危険物は専用の場所に保管することを徹底する
- ロケーション管理を導入する
- 作業フローを考慮した配置にする
順に解説します。
4-1. 危険物は専用の場所に保管することを徹底する
まず最初に、危険物は法令や安全基準に従って、専用の場所に保管することを徹底してください。
保管エリア整理においては、安全性が最優先事項です。
これを怠ると、作業員及び設備にも大きなリスクをもたらす可能性があるため、第一に考えましょう。
危険物とは、安全管理の法律(消防法、労働安全衛生法など)上、特別な取り扱いや保管が必要な以下のような資材のことです。
可燃性の物質
|
爆発性の物質
|
化学性の物質
|
その他の危険物
|
こうした、危険物は高温になりやすい場所を避け、専用エリアを確保して保管することを徹底しましょう。
内容物や危険性が一目で分かるように明示しておくことも重要です。
適切な管理が事故防止と、安全な作業環境の維持に繋がります。
4-2. ロケーション管理を導入する
保管エリアの整理には、ロケーション管理を導入しましょう。
ロケーション管理とは、物品や商品(この場合は資材)の保管場所を番号、番地化する保管方法です。
この管理方法を取り入れることで、エリア(倉庫)のどこに、どの資材があるのかが格段に把握しやすくなります。
具体的には、棚やラックの1段づつにロケーションを振る「区画分け」から始めましょう。
ロケーションは、倉庫内の住所と思ってください。
ロケーションを聞けば、倉庫のどの辺りなのかが分かるように、基本は「列・連・段」で振り分けていきます。
ご参考までに下記の画像をご覧ください。
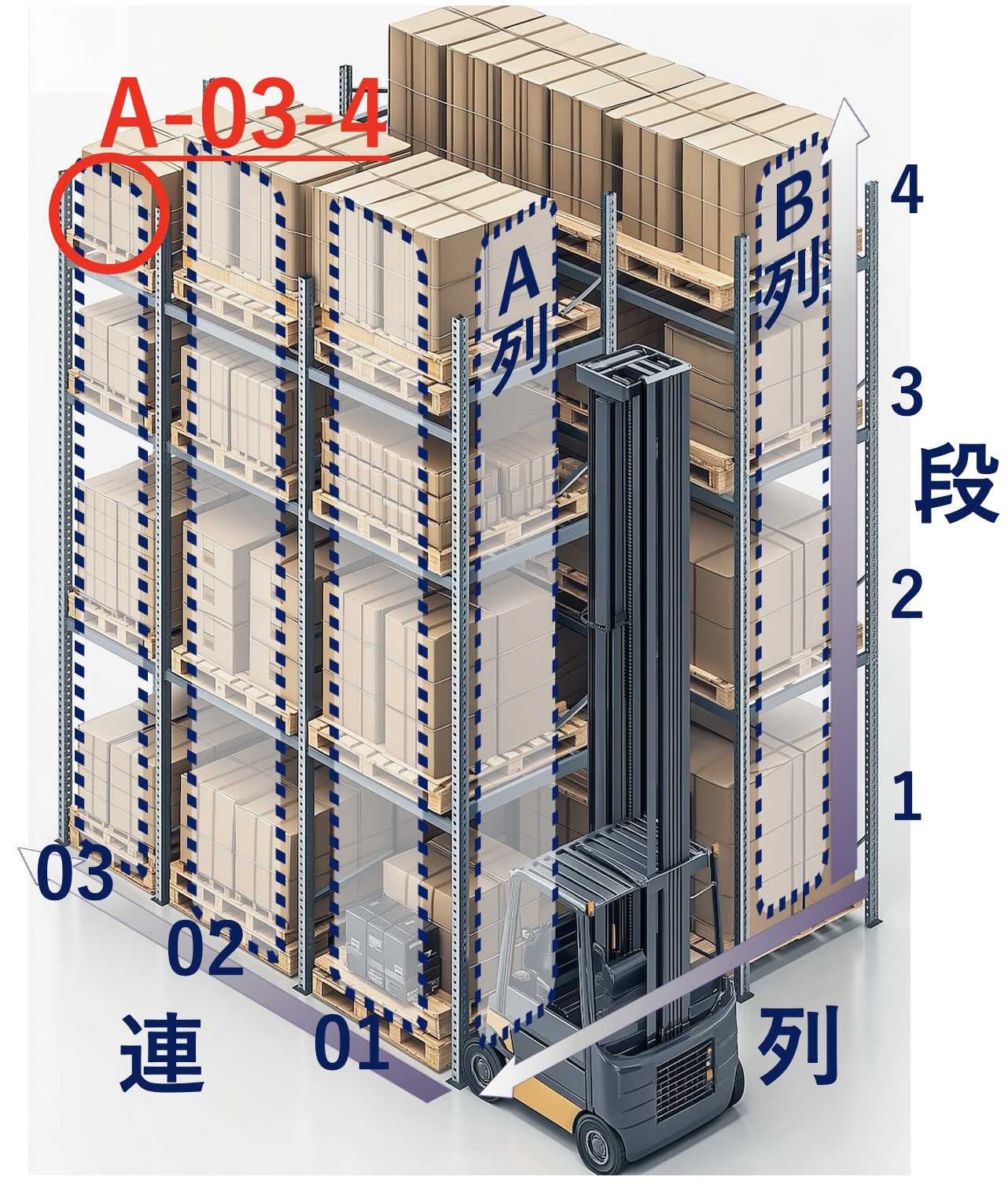
一例ですが、赤丸の位置のロケーションは、列連段の順に表記すると「A-03-4」になります。
区画分けの際には、実際の棚やエリアごとにラベルや標識を付けておくと便利です。
平置きの場合は、一定のエリア毎に床に線を引いてロケーションを付けるのも一案でしょう。
資材がどこにあるかを早く、正確に把握することは、管理効率、業務効率を大きく向上させます。
4-3. 作業フローを考慮した配置にする
保管エリアの区分けでおすすめしたいのは、作業フロー(作業の流れ)に重点を置いた配置です。
作業フローを考慮することで効率が上がり、日常業務の時間短縮が可能になります。
具体的には、以下の2点を念頭に置いて配置すると良いでしょう。
|
|
このような配置を心がけることで、在庫管理が効率化し、作業現場のスムーズな運営を支えることができます。
全体の生産性向上にも貢献できるでしょう。
チェック!環境条件にも配慮しよう |
---|
資材保管の際は、環境条件に配慮することも怠れません。 具体的には、劣化のリスクが高い資材を適切に保管することで、品質を維持し、廃棄ロスを防ぐことができます。 留意点は2つです。
資材の特性に合わせて、管理する環境条件も今一度見直してみましょう。 |
5. ステップ4:資材の発注方式を設定する
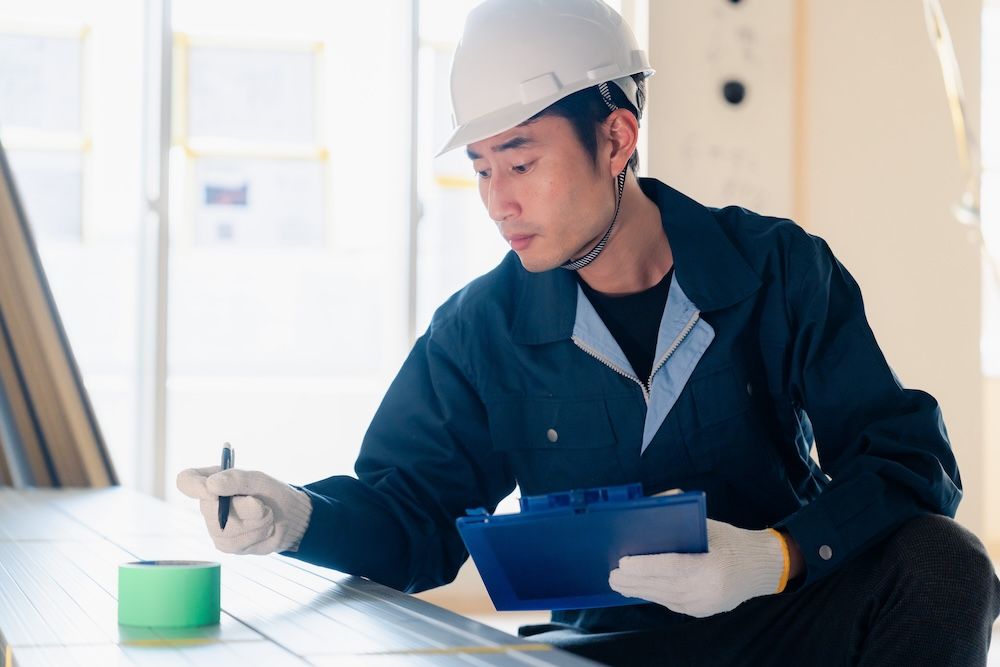
次に、自社に適した資材の発注方式を設定しましょう。
資材の発注方式を適切に設定することは、効率的な在庫管理とコスト削減につながります。
発注方式は、大きく分けて2つありますが、どちらか一方を選ぶというのではなく、資材の特性や使用状況に応じて、使い分けると良いでしょう。
- 定量発注方式
- 定期発注方式
それぞれの特徴と注意点を示した下表をご覧ください。
【定量発注方式】 在庫が一定数を下回った時点で発注する方式。 この方式は、安定した消費量が見込める資材に向いていて、必要最低限の在庫を維持しやすいのが特徴です。 <定量発注方式を設定するメリット>
※定量発注方式では、必要最低限の在庫量(安全在庫量)が設定され、在庫量がその基準を下回った時点で自動的に発注が行われます。 <注意点> |
【定期発注方式】 決まった周期ごとに在庫を確認し、必要に応じて発注する方式。 この方式は、不規則な消費パターンがある資材や、多くの種類を一括で管理する場合に便利です。 <定期発注方式を設定するメリット> |
設定の使い分け例 |
---|
|
いずれの方式を採用する場合でも、発注プロセスを明確化し、関係者間で共有しておくことが重要です。
適切な発注方式を設定することで、資材不足や過剰発注を防ぎ、運用効率を向上させることができます。
6. ステップ5:定期的に見直しをする
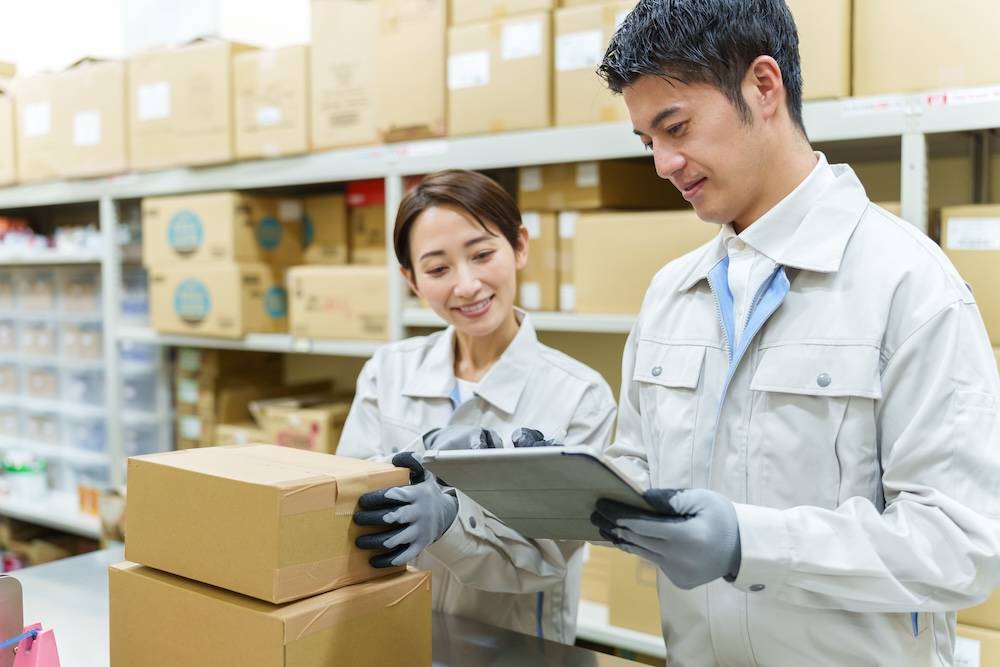
体制が整った後は、在庫管理の運用が効率的に行われているか、定期的にチェックすることが重要です。
具体的には、以下のことを実施しましょう。
※棚卸しの頻度は毎月がおすすめです 毎月定期的に棚卸しを行うことで、迅速にズレを発見し、適切な対策を講じることができます。 |
|
|
定期的な見直しを行うことで、在庫管理の無駄や不足を防ぎ、効率的で安定した運用が可能になります。
このように、定期的な見直しを行うことで、在庫管理の無駄や不足を防ぎ、運用体制を改善していくことができます。
7. 「在庫管理システム」の導入で長期的な安定管理を実現しよう
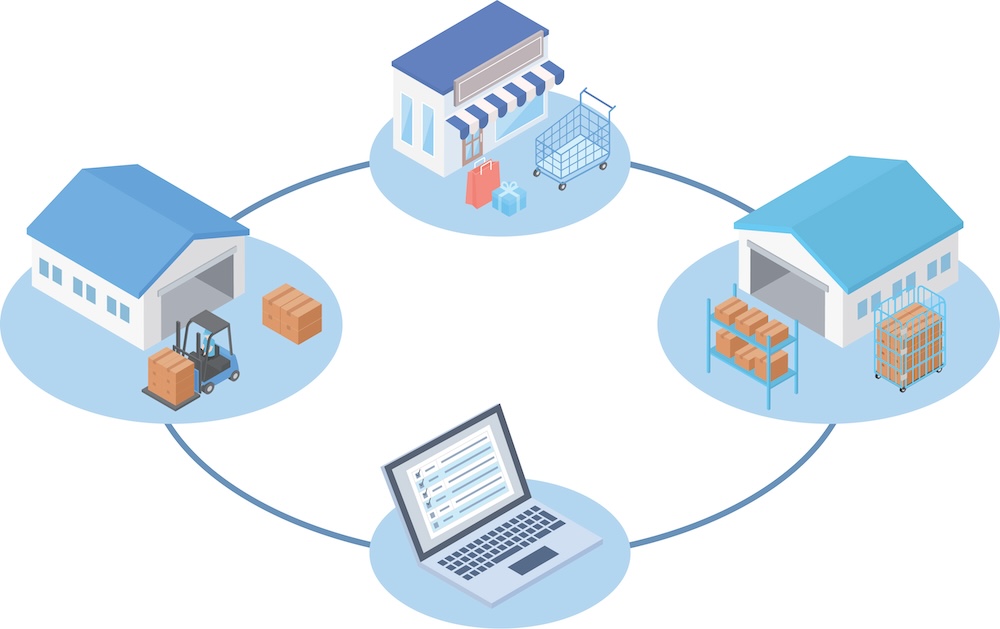
さて、ここまで建設業での一般的な在庫管理の流れを紹介してきましたが、さらに効率化を図るために考えたいのが、システムを活用した在庫管理の自動化です。
在庫管理システムを導入することで、管理の精度が飛躍的に向上し、ここまでの作業がさらに効率的に進められるようになります。
「在庫管理システム」導入で実現できることは、以下の通りです。
「在庫管理システム」導入で実現できる6つのこと |
---|
1.リアルタイムの在庫管理 クラウド上で在庫データを常時更新・共有するため、どの現場にどれだけの在庫があるのかを瞬時に把握可能になります。これにより、在庫不足や過剰在庫といった問題を防ぐことができます。 |
2.情報の一元管理と現場間の共有 複数の倉庫や拠点がある場合でも、システムを使えば在庫情報を一元化。どの現場でも最新情報を共有でき、情報の行き違いや更新漏れがなくなります。 |
3.在庫管理の自動化 入出庫データの入力や棚卸作業が自動化され、人的ミスが大幅に削減されます。これにより、業務の精度が向上するだけでなく、作業時間も短縮されます。 |
4.資材の品質管理 特定の資材の状態や品質をシステムで追跡できるため、不良品や品質トラブルの発生を未然に防ぐことが可能です。 |
5.保管期限や使用期限の管理 賞味期限や使用期限がある在庫もシステムが自動で通知してくれるので、期限切れによる廃棄やトラブルを防ぐことができます。 |
6.データ分析による必要在庫数の予測 過去データ(在庫状況、使用履歴、発注履歴など)をシステムで蓄積、分析することで、季節ごとの需要や工事進行状況に基づいた必要在庫数を予測することができます。これにより、過剰な在庫コストを削減し、効率的な発注計画を立てることが可能になります。 |
在庫管理システムを導入することで、在庫数や動きが一目で分かり、必要な情報をすぐに確認できるようになります。
在庫データをクラウド上で一元的に管理し、リアルタイムで情報を共有することも可能です。
現在、建設業の在庫管理では「紙ベースの管理」「Excelへの依存」「情報のリアルタイム共有の不足」といった課題が浮き彫りになっています。
紙ベースの管理による問題→人的な記録忘れ、数量間違いなどのミスが避けられない |
Excelへの依存による問題→複雑化する在庫管理に対応しきれなくなったり、業務が属人化しやすい傾向があるため、引き継ぎが難しくなったりする |
情報のリアルタイム共有の不足による問題→紙やExcelの管理では情報がリアルタイムで共有できないため、在庫状況の理解にタイムラグが生じる。在庫の無駄や不足による遅延で、現場全体の効率が低下する可能性がある |
こうした問題を一気に解消できるのが、使いやすい「在庫管理システム」なのです。
デジタルツールと聞いただけで、
「なんだか難しそう」
「操作を覚えられるか不安…」
と思われるかもしれませんが、在庫管理システムは、普段使っているパソコンやスマートフォンからインターネットを通じて利用できるもので、操作には特別な知識や技術は必要ありません。
システム化することで、在庫管理の負担やストレスが大きく軽減されますので、ぜひ導入を検討してみてください。
<こちらの記事もおすすめ>
建設業における在庫管理とは?5つの管理プロセスを分かりやすく解説
現場を知っているエルラインの「在庫管理システム」
|
---|
![]() 専門工事事業の実績を持つエルラインは、DX(デジタルトランスフォーメーション)を通じて建設業界の中小企業経営を支援し、経営を安定化する様々なサービスを展開しています。 【LPRE(エルプレ)】 自社の資産でもある資材の数量をいつでもどこでも把握できる在庫管理システム。オンラインで受注管理をおこなえるため、Excelや紙による管理が不要になり、従来の管理業務にあったさまざまな負担を解消します。 ![]() LPRE(エルプレ)の詳細をみる 建設事業を行っているエルラインだからこそ、実際の現場で働く人の目線に立って本当に必要なシステムを開発することで、現場レベルのDX化を実現可能にしています。在庫管理でお悩みなら、現場で働く人のためのイノベーションを推進するエルラインのシステムをご検討ください。 |
8. まとめ
資材の在庫管理は、以下のステップで行いましょう。
- ステップ1|資材の在庫リストを作成する
- ステップ2|リストを元に資材を分類する
- ステップ3|在庫の保管エリアを区分けする
- ステップ4|資材の発注方法を設定する
- ステップ5|定期的に見直しをする
それぞれのステップでは、適切な分析手法の活用や、保管エリアの安全性確保などのポイントを押さえることが重要です。
また、在庫回転率を意識することで、不要な在庫の削減やコストの最適化にもつながります。
記事を参考に、自社に最適な在庫管理方法を見つけ、業務の効率化を目指していただけたらと思います。
コメント