「倉庫管理って結局何をすればよいのだろう?」
「うちの会社でもやっぱり倉庫管理を行うべき?」
倉庫管理の必要性を漠然と感じつつも、自社で実施するとしたら何を行えばよいのかのイメージが湧かず、お困りではありませんか?
倉庫管理とは、倉庫内のすべての業務をマネジメントすることです。
大まかに以下の5つの業務から成り立っています。
- 在庫管理業務
- 入出庫管理業務
- ロケーション管理業務
- レイアウト管理業務
- 人員配置業務
倉庫はバックヤードでありながら「ビジネスの土台」であるともいえ、倉庫管理が適切に行われているかどうかが提供するサービス全体の品質を大きく左右することにもなります。
しかし、重要な役割を担う倉庫管理業務において、業界や業種によっては
- 裏方業務であるために、その重要性が認識されづらい
- 他部門から、業務の複雑さや影響範囲などの理解が得られにくい
- トラブルがなければそのままでいい、とトラブルが起こってはじめて問題視される
などの傾向があります。
そこで本記事では、倉庫管理業務の概要から倉庫管理を行う方法までを、わかりやすく解説していきます。
この記事を読むとわかること
|
---|
|
お読みいただくことで、倉庫管理業務の全体像や重要性などがクリアになるでしょう。
倉庫管理についての理解を深めたい方、迷っている方、お悩みの方、検討材料が必要な方は、ぜひ最後までお読みください。
1. 倉庫管理とは倉庫内の全作業をマネジメントすること
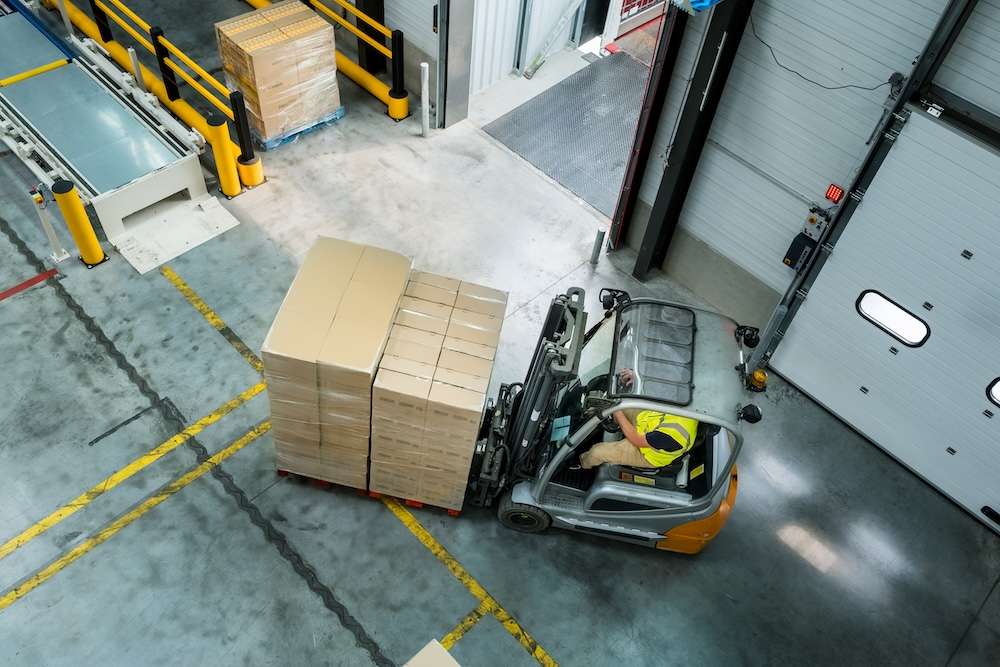
倉庫管理とは、業務効率をアップするために、倉庫内で行われる全ての作業をマネジメントすることで、大きく下記の5つの業務から成り立ちます。
(それぞれの業務の詳細については「3. 倉庫管理の業務内容」で解説しています)
倉庫管理の5つの業務 |
---|
|
倉庫作業は、顧客から預かった荷物を倉庫で保管すること自体をビジネスとする倉庫業のケースを除き、基本的にはバックヤード業務です。
しかし、物品を扱う限り、倉庫管理が適切に行われているかどうかは、企業・法人として提供するサービス全体の品質に大きく影響します。
それは、製造業であれ、小売業であれ、農林水産業であれ、建設業であれ、変わりません。
倉庫作業の管理状況が、倉庫外で行われる業務を支えているということであり、倉庫管理は「ビジネス運営の土台」であるといえるでしょう。
2. 倉庫管理と在庫管理の違い
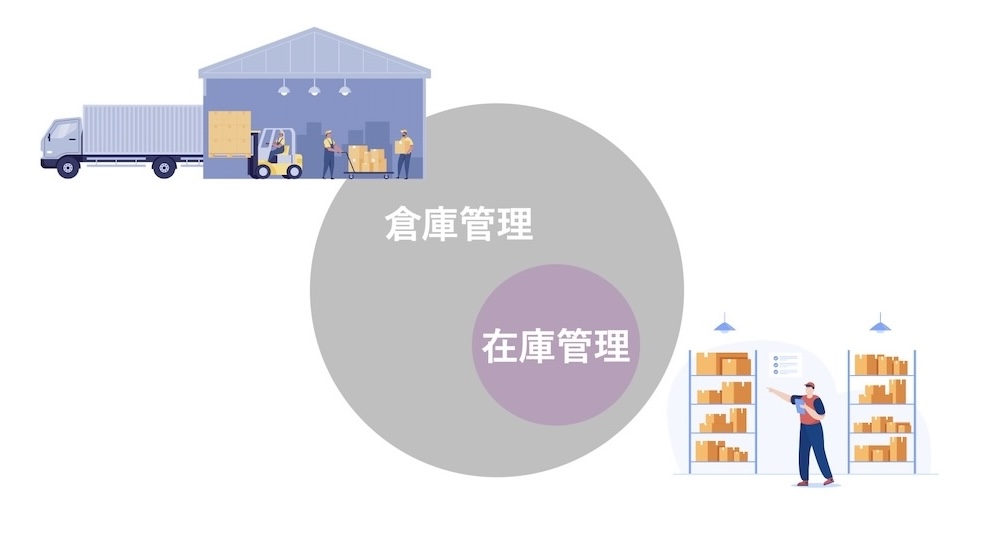
「倉庫管理」と似た言葉に「在庫管理」がありますが、在庫管理は倉庫管理を構成する業務の一つという位置付けです。
この2つの言葉の違いは、文字に見えている通り、管理対象が「倉庫(での作業)」なのか「在庫」なのかという点であり、在庫管理の管理対象はより限定的なのです。
また、それぞれを実施する目的も異なっており、在庫管理の目的が利益率アップである一方、倉庫管理の目的はサービス品質の維持・向上となっています。
まとめると下表のようになります。
項目 | 倉庫管理 | 在庫管理 |
---|---|---|
管理する対象 | 倉庫内で行う全作業 | 倉庫内にある在庫 |
管理の主な目的 |
サービス品質の維持・向上
|
利益率アップ
|
3. 倉庫管理の業務内容
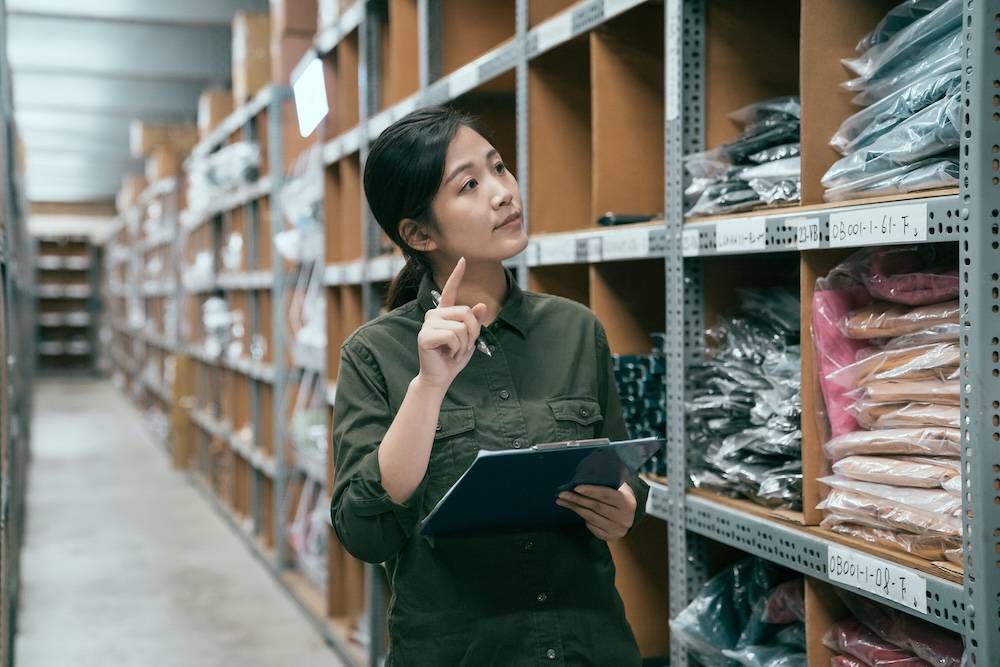
倉庫内の全業務を対象として行う倉庫管理は、前述の通り、主に次の5つの業務から成り立っています。
- 在庫管理業務
- 入出庫管理業務
- ロケーション管理業務
- レイアウト管理業務
- 人員配置業務
それぞれについて、以下で詳しく解説します。
3-1. 在庫管理業務
倉庫内の在庫品の数量や状態を管理する「在庫管理業務」は、倉庫管理の業務の中でもかなりの比重を占める業務です。
生産準備が万全でも、原材料が不足していれば製造できません。
山ほど受注していても、製品が棚に並んでいなければ出荷できません。
だからといって在庫を多めに持てばよいという話でもなく、余剰在庫は有限な保管スペースを占領し、特に倉庫を借りている場合にはコストがかかり、売れ残れば損失となるリスクです。
常に多過ぎず少な過ぎない在庫を持つように、コントロールする必要があるのです。
つまり、できるだけ余分な在庫は抱えず、必要となるタイミングに合わせ必要な数量だけきっちり確保するというのが在庫管理の基本スタンスです。
そうした基本スタンスに則った調整を的確に行うには、高い精度での在庫管理が欠かせません。
在庫管理の考え方の代表格が「かんばん方式」 |
---|
トヨタ自動車株式会社の生産管理方式の一環である在庫管理方式が「かんばん方式」です。 ‘Kanban’ Methodとして世界的にも通用する言葉となっています。 今日では製造業に限らず広く活用されていますが、もともとは部品名・品番・保管場所などが記載されたプレートを発注書や受領書の代わりに用いて、製造工程間での部品の納品・引き取りを行う手法です。 前工程で生産された部品が後工程で使われますが、後工程で使った分だけ前工程で生産して補充するという、いわば「意図的な自転車操業」であり、無駄な在庫を極限まで減らす手法といえます。 コロナ禍では、部品供給が滞って生産に支障をきたす事態が起きたため、やや多めの安全在庫(バッファとして確保しておく在庫)を持っておくことが必要という考え方も出てきました。 しかし前述の通り、在庫を持ち過ぎた場合、コスト増大や、スペースを有効活用できないことによる機会損失、現金化できないことによる資金繰りの悪化などを招きかねません。 そのため、「在庫はできるだけスリムに」という考え方がやはり根強いです。 |
3-2. 入出庫管理業務
製品・資材を倉庫に入れたり、逆に保管していたものを倉庫から出したりといった製品・資材の動きを記録して把握する「入出庫管理(入出荷管理)業務」も、倉庫管理の重要な業務の一つです。
入出庫管理業務をひと言で言えば「製品・資材の出入りを記録に残す」ということになりますが、単に記録するということではなく、それを支える複数の作業が存在します。
入庫時に行う作業 | 出庫時に行う作業 |
---|---|
・積卸し作業(トラックやコンテナからの荷物の積みおろし) ・検収作業(入荷した品に問題がないかの確認) ・検品作業(品目と数量の確認) ・棚上げ(棚入れ)作業(決められた棚への保管) ・記録作業(入庫内容の記録・入力) 等 | ・ピッキング作業(必要な品の保管場所からの取り出し) ・検品作業(品目と数量の確認) ・梱包作業(指定の荷姿への取りまとめ) ・仕分け作業(出荷方面別・出荷先別・品目別・配送業者別などでの分類) ・積込み作業(トラックやコンテナへの荷物の積込み) ・記録作業(出庫内容の記録・入力) 等 |
これらの作業を正確に行うことで、入出庫管理が成立します。
入出庫管理がおろそかになっていると、
「見込んでいた数量を確保できない」
「あの製品が今どこにあるかがわからない」
といった問題が起こりかねません。
在庫状況の把握ができず、在庫管理の精度に影響します。
品質問題が発覚しても、当該の商品の追跡を行えず、迅速に対応することができません。
棚卸しの際にも、棚卸差異(帳簿上の在庫と実在庫とのズレ)が発生し、さらに追加の工数が発生してしまいます。
たとえ今のところは大事に至らずに済んでいるとしても、いずれ大問題につながるのを避けるために、入出庫管理を適切に行う必要があります。
3-3. ロケーション管理業務
各保管場所に所番地(ロケーション番号)を割り振り、ある品がどこに保管されているかがすぐにわかるようにするのが「ロケーション管理業務」です。
たとえば、「倉庫に入って向かって右側の棚の上のほう」といったざっくりとした情報では、いざ製品・資材が必要となった際にすぐに見つけられるとは限りません。
目的の品をスムーズに見つけられるよう、
- どのエリアか
- 何列目の通路か
- いくつ目の棚か
- 棚の何段目か
- 何個目の間口(保管スペースの区切り)か
といった情報を示す「03-A-101」などの所番地で保管場所を明確に示すようにするのです。
ロケーション管理の方式は3種類あります。
【フリーロケーション】 入庫の都度、任意の場所に順次格納していき、ハンディターミナル(携帯端末)でバーコードを読み取ることで所番地を登録する方式 【固定ロケーション】 保管場所を品目別に決めておき、常に決められた場所に格納する方式 【ゾーンロケーション】 関連品目をエリアごとに集約した上で、同エリア内での管理方法にはフリーロケーションを採用する方式 |
各方式の特徴を下表にまとめました。
フリーロケーション | 固定ロケーション | ゾーンロケーション | |
配置場所の自由度 | ◎ | × | △ |
ピッキング(熟練度) | 熟練度は問われない | 熟練するほど生産性が高くなる | 熟練度が多少影響する |
ピッキング(移動距離) | × | ◯ | ◯ |
所番地の割り振り作業の負担 | ◎ 割り振りのし直し不要 | × 新商品入荷や廃盤のたびに再割り振りが必要 | ◯ 売れ筋が変わればエリア単位での再割り振りが必要 |
システム導入 | × 導入必須 | ◯ 必ずしも導入は必要ない | × 導入必須 |
向いているケース | ・在庫量の増減が激しい ・入れ替え頻度が高い ・小型商品を少量ピッキングする場合が多い ・保管品の種類が多い | ・年間を通して在庫量があまり増減しない ・入れ替え頻度が高くない ・在庫を切らさないことが重要(医療品など) ・保管品の種類が少ない | ・自動倉庫に保管されている ・出荷頻度の高い製品を大量に扱い、補充エリアが必要 |
フリーロケーションのピッキング効率を上げる「ダブルトランザクション」 |
---|
フリーロケーション方式を採用した場合、ピッキング時の効率を考慮した配置とならない、同一の商品が点在することがあるなどの理由により、ピッキング作業の効率が落ちてしまう場合があります。 このデメリットを解消するのが、保管専用のストックエリアと、ピッキング専用のピッキングエリアとを分ける「ダブルトランザクション」という運用方法です。 ひと通りの物品を数日分だけ手前のピッキングエリアに出しておき、それ以外の在庫は奥にあるストックエリアに残しておきます。 こうすることで、ピッキング作業がピッキングエリアという限られたスペース内で完結するため、複数の品をピッキングする場合にも移動が最小限で済み、素早く終えられます。 物品をストックエリアからピッキングエリアへと移す作業こそ発生しますが、ピッキング所要時間を短縮のに効果的な方法です。 |
3-4. レイアウト管理業務
倉庫内のレイアウトを最適化するのが「レイアウト管理業務」です。
レイアウト対象には次のようなものがあります。
レイアウト管理業務における管理対象の例 |
---|
|
レイアウト管理が適切ならば、「特定の棚の前がいつも混み合う」「台車置き場が遠過ぎるせいか台車が返却されないケースが多発」といったようなことも起こらず、倉庫作業の効率が上がります。
レイアウト管理の良し悪しが特に影響するのがピッキング作業で、レイアウトに問題があると、
- 作業員が右往左往してしまう
- 出入口付近で作業者同士がぶつかってしまう
- 移動距離がやたらと長くなってしまう
といった状況に陥ります。
逆に、合理的で機能的なレイアウトが実現されていれば、
- 作業者の動線が一筆書きになり、通路が実質的に一方通行となる
- どの通路においても渋滞が発生しない
- 各作業員の移動距離が最短となる
といった状況が生まれるはずです。
倉庫内のレイアウトは、「回転率の高い品の保管場所を取り出しやすい位置にする」などの基本原則のほか、現稼働状況、さらには将来予測まで考慮して決める必要があり、手間と時間がかかります。
しかし、基本的に頻繁に変更するものではなく、最適なレイアウトを一度実現してしまえば、その後は効率化の恩恵を享受し続けることができるので、レイアウト設計にぜひ注力したいところです。
ピッキング作業の「7つのない」を実現できるレイアウトを目指す |
---|
レイアウトの最適化に当たっては、ピッキング作業で意識すべき7つの「ない」を念頭に置くと、効率的なレイアウトが実現するでしょう。 7つの「ない」とは、下記の通りです。 待たせない:ピッキング通路に「渋滞」などが発生し、手待ち、待機などが多発する状況は回避する 歩かせない:ピッキング通路の動線が必要以上に長くなり、作業者の歩行量が増えないようにする 持たせない:ピッキング作業にあたって、ピッキングリスト、スキャナーなどの他に余計な持ち物がないようにする 考えさせない:「次は何をするのだろうか」といった疑問を作業者に抱かせず、スムーズに作業ができる環境にする 探させない:ピッキングの際などに作業者に探させないようにする 聞かせない:作業者が自分の作業について頻繁に質問しないようにする 書かせない:作業者が複雑なメモ書きなどを行わないようにする (鈴木邦也、『入門 物流(倉庫)作業の標準化』、日刊工業新聞社、2020年、64ページより引用) 上記の「7ない」を念頭に置いて設計された理想的なレイアウトによりスムーズなピッキングが可能となれば、ピッキングのミスが原因の誤出荷も減るはずです。 |
3-5. 人員配置業務
倉庫管理において想像以上に重要な業務が、「人員配置業務」です。
システム化された自動倉庫でない限り、マテハン機器(省人化を目的として物品の移動・搬送に用いる機械)を活用するとしても、倉庫作業に作業員が介入しないわけにはいかないからです。
下記のような点を考慮して、最適な人員配置を行います。
人員配置において考慮すべきこと |
---|
(*人時:作業者1人が1時間でこなせる作業量) |
「ピーク時なのに必要な人数を確保できない」といったことのないよう、よく考えて人員を配置します。
4. 適切な倉庫管理で実現する2つのこと
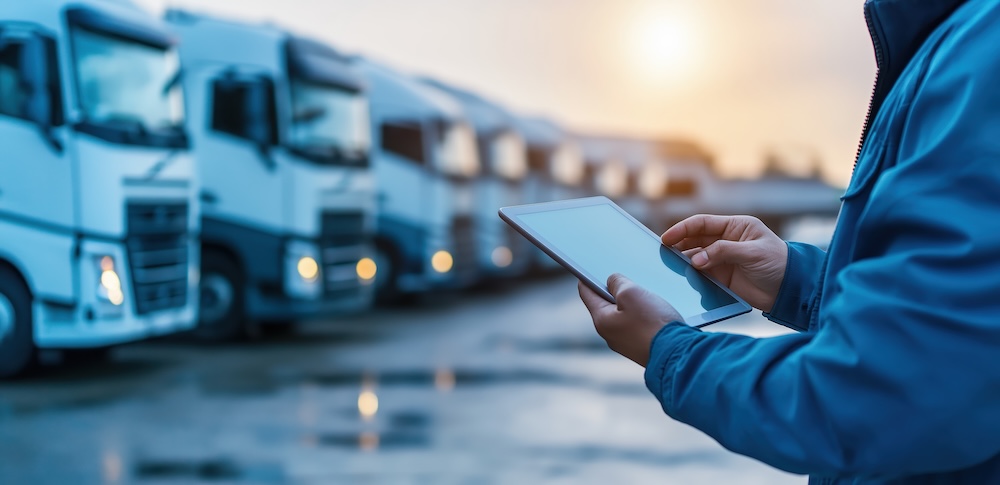
在庫量や入出庫状況、保管場所、人員配置と倉庫内のあれこれをひっくるめてコントロールする倉庫管理業務。適切に行われていれば、次の2つのことが実現します。
|
それぞれについて、以下で簡単に説明します。
4-1. 利益率が改善される
適切な倉庫管理は、以下の2つを可能にします。
結果として、利益率が改善されます。
- 在庫の過不足がなくなり、売上減少や余計なコストの発生がなくなる
- 製品・資材の管理に関わる工数が大幅に減り、人件費を削減できる
何がどれだけあるか、どこにあるか、いつ出ていっていつ入ってきたかが常にクリアになるため、正確な在庫量を把握できれば、適正な発注を適時に行えます。
「心配だから多めに確保しておこう」といった不安に駆られての調達や、逆に「この辺まで減らしても問題ないだろう」といった勘による調整よりもずっと的確な判断が可能で、無駄が出ません。
また、各作業が合理的かつ効率的な手順で行われるようになる結果、たとえば下記のような効果が見込まれ、余計な工数がかからなくなるはずです。
- 誤出荷や出荷遅延などが減って、「しなくてもいい作業」が発生しなくなる
- 必要な品がどこに保管されているかわからず探し回ったり、狭い通路を複数の作業員が行き交うことによる渋滞が発生したりすることがなくなる
4-2. 顧客満足度が向上する
適切な倉庫管理を行うことで、顧客満足度の向上も期待できます。
なぜなら、経験や勘、憶測、目分量といった確度の低い根拠ではなく、正確でタイムリーな情報に基づいて在庫を管理できるようになるため、
「注文したのに品切れだった!」
「在庫状況を問い合わせたのに、すぐに回答が来ない」
といった顧客の不満を減らすことができるからです。
たとえば、倉庫にある製品・資材の正確な数量や、いつなら対応できるかがわからず、見当をつけて受注したものの、実際には間に合わせられないと判明して、平謝りするようなことがなくなります。
逆に注文依頼があっても即答できないといったこともなくなりますので、機会損失を防ぐ効果もあります。
5. 【事例】適切な倉庫管理を行うことによる成果
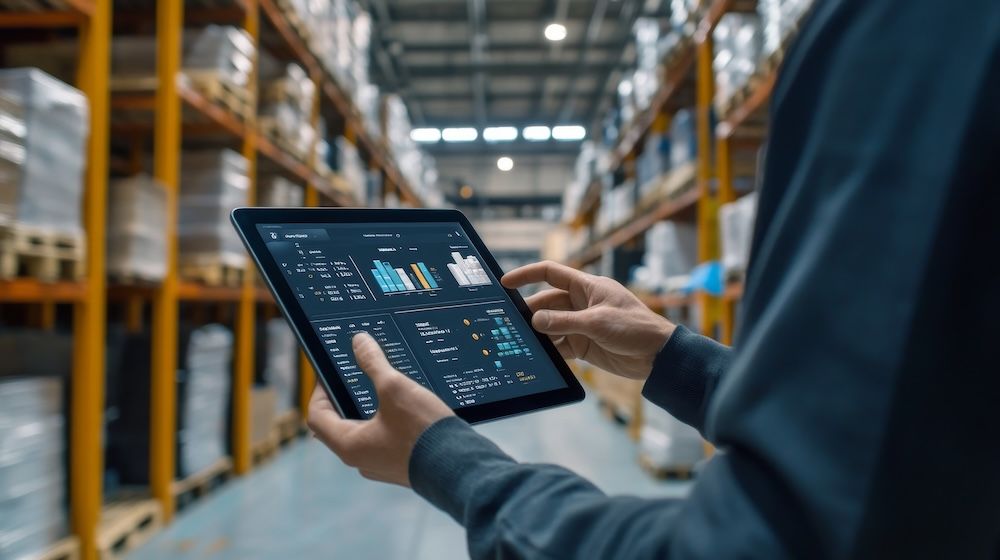
前章でご紹介したようなメリットのある倉庫管理を行うべきとは漠然と思っても、どの程度の導入レベルでどのくらいの改善が見込めるのか、現場がどう変化するのかをイメージできないかもしれません。
そこで本章では、倉庫管理を行うことでどういった改善が見込めるのかをリアルにイメージできるよう、実際の事例をもとにまとめた「こんな風に変わる!」という典型例をご紹介します。
5-1. 管理・指導役の配置でルールが徹底されるようになり作業品質向上
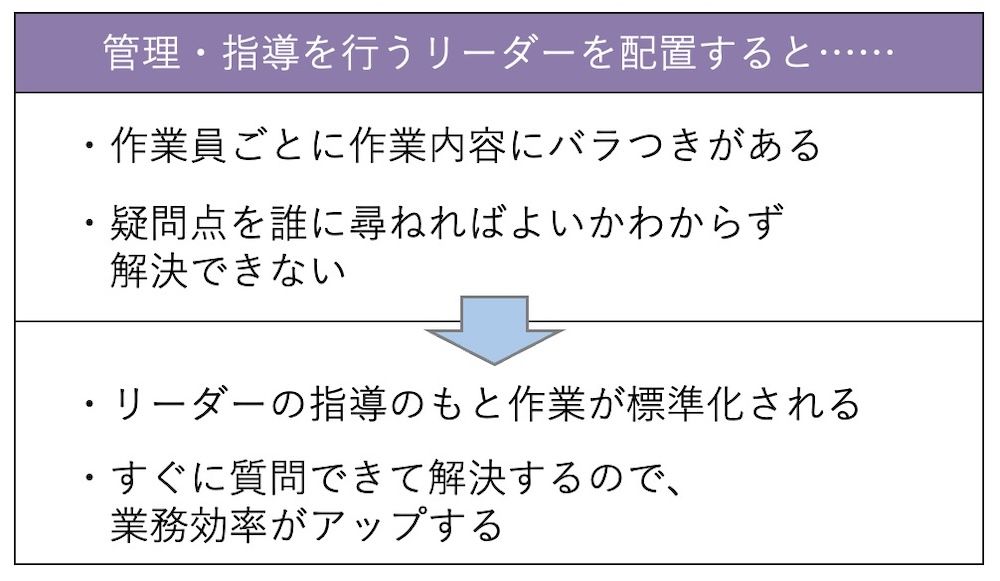
作業ルールの徹底を目的として、管理・指導を行うリーダー(できれば専任者)を配置することで、作業品質の向上が見込めます。
たとえ作業手順書は用意されていても、現場では個々の作業者が自分のやりやすいやり方で作業しているというケースは多いからです。
そうした場合、一つひとつの作業に着目する限り特に問題はなくても、作業内容にバラつきがあることで、倉庫作業全体としては非効率的になってしまっているものです。
たとえば、作業者により検品の手順も熟練度も異なるという前提に立った作業標準化ができていないと、検品ミスをどうしても防ぎきれません。
現場での作業に目配りし、必要に応じて「2人1組で指差呼称(指差し確認)して検品してくださいね」と指示する人を配置すれば、検品精度はグンと上がるはずです。
また、「積卸しの際に荷台上で手作業するのは危険なので、フォークリフトに任せるために、トラックはこちらの場所に停めてください」と誘導する人がいれば、事故の誘発を防げます。
そのように、「作業ルール徹底の旗振り役」を配置すれば、業務品質が向上するだけでなく、わからないことがあったときに尋ねるべき相手も明確になるため、業務効率もアップするでしょう。
5-2. 倉庫内のレイアウトの見直しで人件費削減
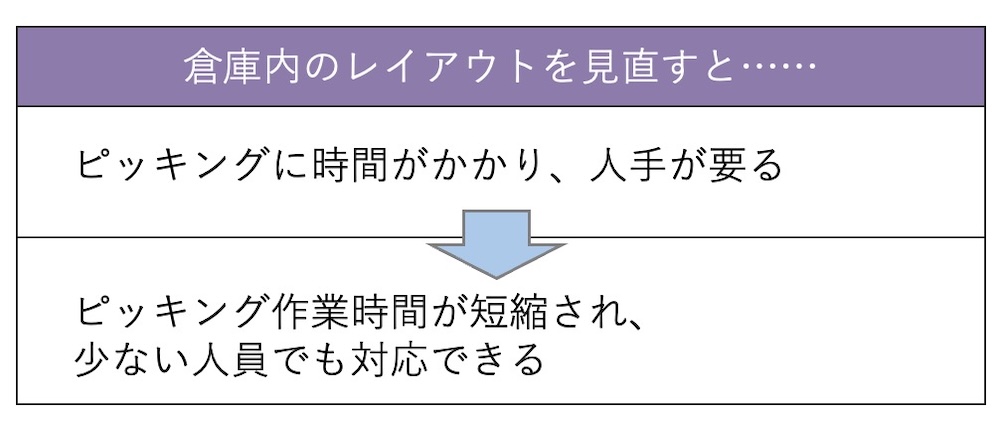
倉庫内のレイアウトを見直すことで、人件費削減を見込めます。
考え抜かれたレイアウトはピッキング作業時間の短縮につながり、従来通りの作業量をより少ない人員でこなせるようになるためです。
具体的には、たとえば次に挙げるような改善策を実行します。
- 棚配置を受注頻度順とし、受注頻度の高い商品の棚を作業開始位置付近に集約
- 動線を遮ってしまう設備類を撤去
- 作業員の渋滞防止のための進行方向取り決め
人件費だけでなく、物流トータルコストの削減もおおいに期待できるでしょう。
5-3. 在庫管理業務へのシステム導入で数量確認の精度と効率の大幅アップ
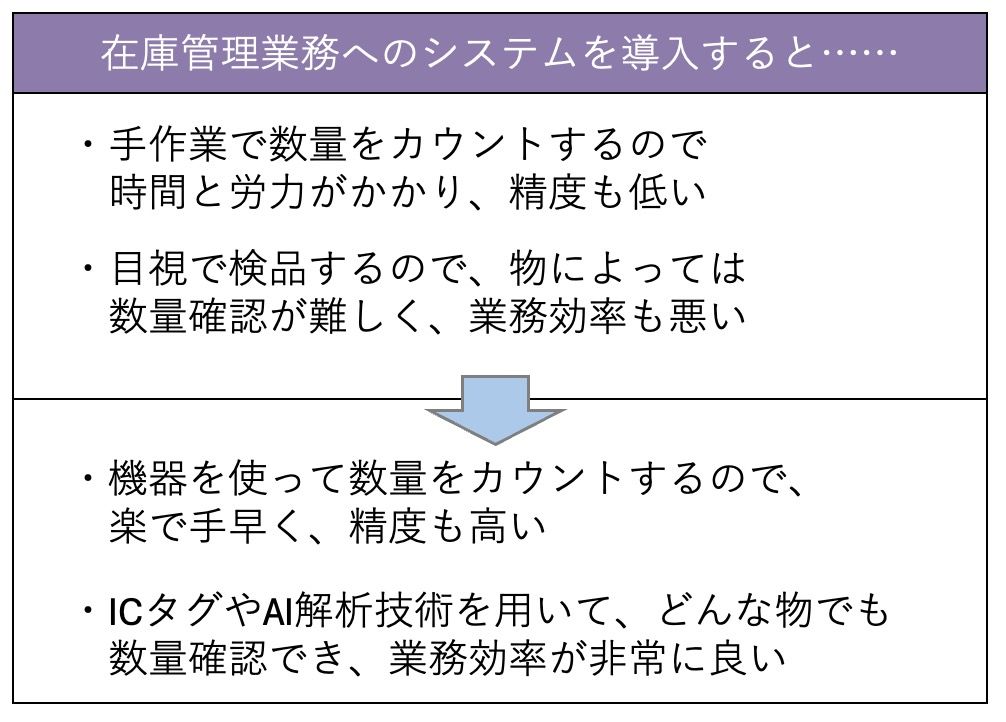
在庫管理業務にシステムを導入することで、製品・資材の数量確認が楽に、手早く、しかも正確に行えるようになります。
最新技術により、人手に頼らない数量カウントが可能となるからです。
扱う物品によりますが、出荷時や返却があったときに目視で数量確認することが難しいケースもあります。(重量物、ブルーシートやネットのように面積の広いもの等)
そんなケースで特に役立つのが、物品につけたICタグ(RFID)を専用リーダーを使い非接触で読み取る識別技術や、写真をAI解析して数量を自動カウントする技術なのです。
一括で数量を読み取るそうした技術を採用しているシステムを導入すれば、検品に労力と時間をかける必要がなくなり、業務効率が大幅にアップします。
6. 今すぐ始めるべき!倉庫管理が特に効果的なケース
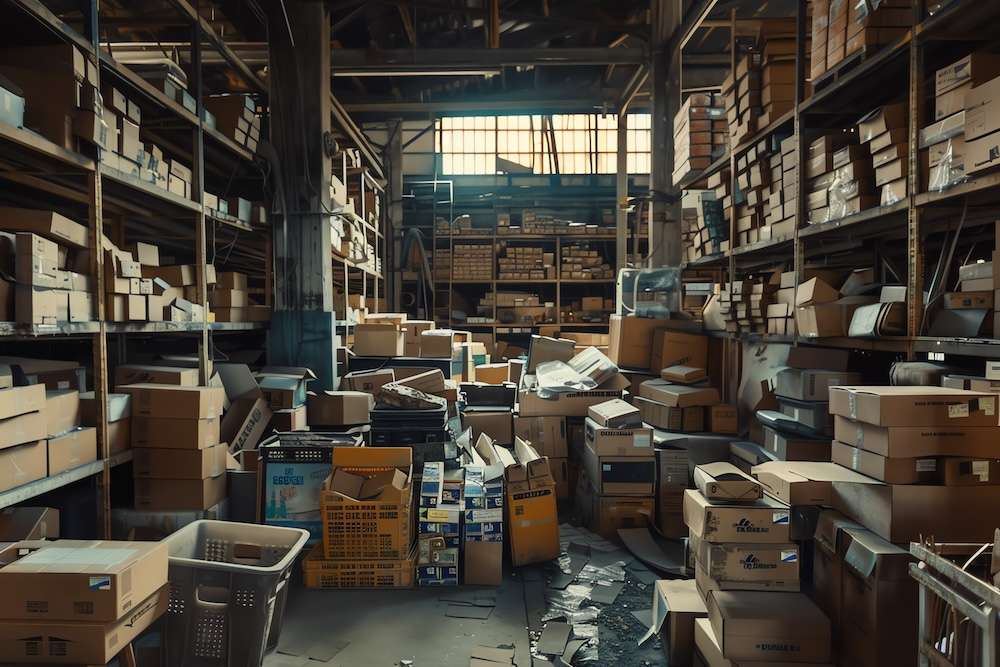
ここまでご紹介してきた倉庫管理は、業種を問わず、倉庫で(あるいは屋外保管場で)製品や資材などを保管している全ての企業・法人にとって必要な対応です。
しかし、企業・法人により状況は異なるため、必要性の度合いは一様ではありません。
本章では、倉庫管理の実施により特に大きな効果がもたらされると見込まれるケースとして、下記の2つをピックアップします。
|
各ケースについて、以下でもう少し詳しく見ていきましょう。
6-1. 商品数が大幅に増えて以来ミスが多発しているケース
商品の種類や扱う数量が増えたことによってミスが多発しているなら、倉庫管理が強く勧められます。
なぜなら、ミスの多発は、「目視で在庫量の見当をつける」「経験と勘に頼って発注タイミングを調整する」といった今までやってきた方法では回っていかなくなっていることを示しているからです。
極端な話、取り扱っている商品が1種類しかなく、数量も少ないのであれば、目視で在庫量を確認することも可能ですし、経験に基づいた運用でもやっていけないことはないでしょう。
しかし、商品の種類や扱う数量が増えれば、話は変わってきます。
倉庫管理という体系的な運用なくしては、もはや手に負えない局面に来ているということであり、それだけに、倉庫管理を実施した場合の効果は大きいといえるでしょう。
6-2. 急な追加受注や適正在庫の維持に対処できていないケース
急な追加受注に対応できない、常に在庫が適正量となるようなコントロールができていないといったケースも、倉庫管理を実施することで大きな改善が見込めるパターンです。
なぜなら、そうしたケースの根底には、在庫状況を把握できていないという状況があり、そのことによってビジネスに支障が出ているからです。
急な追加受注があっても対応できない理由には、今ある在庫では足りないということのほかに、今ある在庫でなんとかなるのか自体がはっきりとはわからないということはないでしょうか?
適正在庫の維持が難しい理由は、どのタイミングでどのくらい減る見込みなのか、あるいは増える見込みなのかを読みきれていないからではありませんか?
毎回「なんとなく見当をつけての判断」をしていると、データが蓄積されていきません。
直近のデータも残っていないから、いつ頃補充されるか、どれだけ補充されるかも正確にはわかりません。
結果として、少しでも「足りないかもしれない」「間に合わないかもしれない」と感じたら、せっかく注文があってもお断りするということになってしまいます。
逆に、大丈夫だろうと注文を受けたものの、読みが甘く、期日に間に合わせられないということもあり得るでしょう。
倉庫管理を行えば、在庫状況や入出庫状況を正確に把握した上で判断できるようになり、こうしたビジネスチャンスの取りこぼしや、信用失墜につながる事態を避けられます。
7. 倉庫管理を行うための2つの選択肢
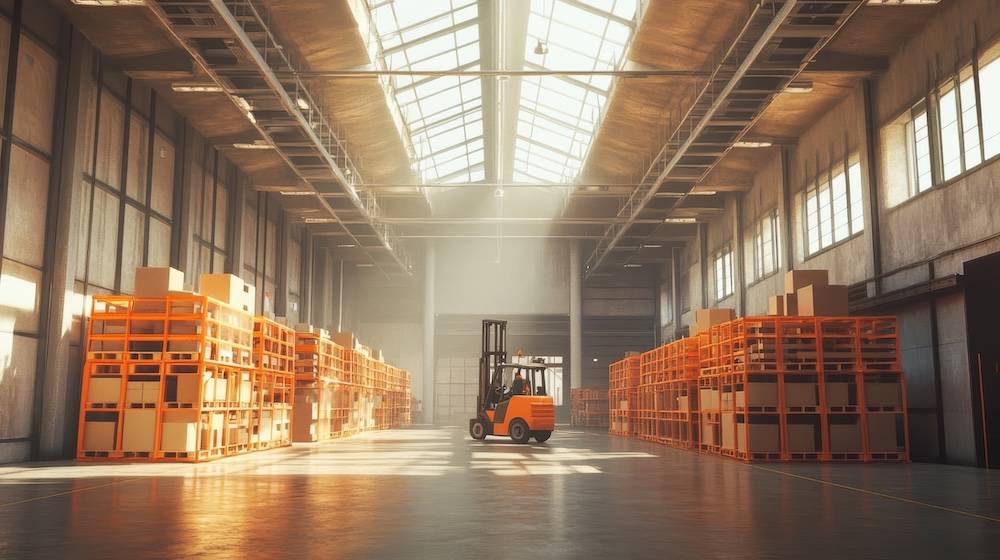
ここまでお読みいただいて、倉庫管理の重要性を再確認し、自社でも実施しようとお考えになった方もいらっしゃるでしょう。
そうした場合の選択肢には、下記の2つがあります。
|
それぞれについて、以下でもう少し詳しく見ていきましょう。
7-1. 倉庫管理の方法1|自社で対応する
倉庫管理のシンプルかつわかりやすい選択肢は、自社で倉庫管理を行うことです。
自社で倉庫管理をする場合は、倉庫管理員を配置しましょう。
倉庫管理業務は多岐にわたるため、各社員ができる範囲で対応するという曖昧な運用ではなく、「倉庫管理を担当する人」を正式に据えないと回っていきません。
なおかつ、何事も一定以上の規模になってくると、兼任者での対応に限界が訪れますので、ごく小規模な倉庫や入出庫の頻度が低い倉庫でない限り、専任の倉庫管理員が望ましいといえます。
配置する人員については、今いる社員を異動させるほかに、新規に人材を雇用することも検討しましょう。
特にビジネス規模拡大や倉庫増設を見込んでいる場合には、倉庫管理に携わるポジションを用意し、そこに入ってもらうための新たな人員を雇用するのがおすすめです。
監督者として雇用するならスタッフマネジメント能力を重視する、倉庫内の実作業に積極的に関わってほしいならフォークリフト運転資格を持っていることを条件に人選すれば、スムーズでしょう。
システム導入もおすすめの選択肢 |
---|
倉庫管理業務の中でも、特に在庫管理業務と入出庫管理業務の部分へのシステム導入は、大幅な業務効率化が見込めるため、おすすめです。 倉庫管理を行なっているにもかかわらず、在庫差異(帳簿上の在庫と実在庫のズレ)がしばしば発生する、誤発注が頻発するといったような状況であれば、アナログ管理に限界が来ているということです。 アナログで運用するには物量が増え過ぎてしまったのかもしれません。 そうした場合、人を追加で配置しても、人為的ミスが増える一方になる未来が予想されますので、先を見越して、システム導入を真剣に検討すべきタイミングといえるでしょう。 また、単に人為的ミスが減るだけでなく、データの蓄積とリアルタイムでの情報共有が可能となることから、倉庫業務全体の生産性の向上もおおいに期待できる点も、システム導入の大きなメリットです。 たとえば、前年の同時期の入荷データなどをもとに出荷量や作業工数を予測しながらシフトを組めるため、効率的な人員配置が可能となります。 つまり、システム導入により倉庫業務のあらゆる面での最適化が容易になります。 なお、システムには各種ありますが、ネット環境さえあればどこからでもアクセスできるクラウド型は、事務所にいなくても現況を確認できるため利便性がより高く、おすすめです。 |
7-2. 倉庫管理の方法2|外部に委託する
倉庫管理をする2つ目の方法は、外部委託(アウトソーシング)です。
外部委託という選択肢が有力候補となるのは、次のようなケースです。
外部委託が有力候補となるケース(例) |
---|
|
各ケースについて、外部委託がおすすめな理由を簡単に見ていきましょう。
◆教育や労務管理の負担が大きい
倉庫管理未経験の社員や新入社員に必要となる教育や労務管理が負担な場合、外部委託のほうが効率的と考えられるからです。
コスト面で多少割高かもしれませんが、欠員が出るたび仕切り直しとなることを考えれば、結局さほど変わらない可能性は低くありません。
◆出荷量の波が大きい
倉庫業務の繁忙期と閑散期の波が大きい場合、必要な作業員数も時期により大きく変わってくるからです。外部委託なら、短期雇用をこまめに繰り返して人数調整する必要はなく、人件費の負担は必要な分だけで済むでしょう。
◆テレワークを推進している
倉庫作業員は、いわゆるエッセンシャルワーカーであり、現場に出なければ仕事にならないからです。全社的にテレワークを推進している場合、外部委託は、倉庫業務のために出社せざるを得ない例外社員を作らないための選択肢です。
◆倉庫まわりのことは切り離し、本業に集中したい
物流業や倉庫会社でない限り、倉庫業務はあくまでバックヤード業務だからです。本業に注力したいと考えるのであれば、外部委託が解決策となるでしょう。
建設業の在庫管理システムなら、「LPRE」にお任せください
|
---|
![]() 建設業の在庫管理システムなら、現場革命を牽引するエルラインの「LPRE」にお任せください! 倉庫業務の効率化、生産性の向上のために欠かせない「在庫状況や稼働状況、取引状況の可視化」を実現します。 ![]() 「LPRE」の主要機能は以下の通り。一般的な在庫管理システムに搭載されている機能は網羅しています。 ・入出庫管理機能 ・在庫一覧機能 ・在庫検索機能 ・発注管理機能 ・在庫分析機能 ・在庫アラート機能 ・減価償却計算機能 その他、LPREならではの強みと言えるのが、下記3つの機能です。 過入庫管理機能 「出荷時より多くの資材が返却される」という業界特有の事態が生じた際、「どこの資材センターにどれくらい過入庫があったか」を把握し、トラブルを防ぐ レンタル品の請求管理機能 販売品だけでなく、足場仮設資材などのレンタル品の管理もできる WEBオーダー機能 現場からスマートフォンで必要な資材を発注部門にオーダーできる これらの機能は、2007年の創業以来、とび・土工工事を主軸に様々な現場をこなし続けている弊社だからこそ導入できる「真に現場へ寄り添った機能」であり、痒いところに手が届く仕様となっています。 今後も ・LPRE登録者がどこにいるか探せる「マップ機能」 ・近場で資材の貸し借りを行える「マッチング機能」などの機能を追加し、より一層便利なシステムを目指していく予定です。 建設業に特化したシステムだからこそ、現場に即した仕様ならではの使いやすさをご実感いただけます。まずはお気軽に資料請求・お問い合わせください。 今すぐ資料請求・問い合わせする |
8. まとめ
▼「倉庫管理」とは、倉庫内の全作業をマネジメントすることであり、「在庫管理」は「倉庫管理」の一部である。
▼倉庫管理は、主に次の5つの業務から成り立っている。
- 在庫管理業務
- 入出庫管理業務
- ロケーション管理業務
- レイアウト管理業務
- 人員配置業務
▼倉庫管理を適切に行うことで、次の2つが実現する。
- 利益率が改善される
- 顧客満足度が向上する
▼倉庫管理による業務改善の例としては、たとえば次のようなものがある。
- 管理・指導役の配置でルールが徹底されるようになり作業品質が向上した
- 倉庫内のレイアウトの見直しで人件費を削減できた
- 在庫管理業務へのシステム導入で数量確認の精度と効率が大幅アップした
▼倉庫管理の実施が特に大きな効果をもたらすケースの例には、次のようなものがある。
- 商品数が大幅に増えて以来ミスが多発しているケース
- 急な追加受注や適正在庫の維持に対処できていないケース
▼倉庫管理を行うための選択肢には、次の2つがある。
- 自社で倉庫管理を行う
- 倉庫管理業務をアウトソーシングする
本記事が、倉庫管理の必要性を感じている皆様が、具体的にどうすべきかをイメージ・検討するための材料となり、貴社の倉庫管理業務の成功の一助となりましたら幸いです。
参考:物流倉庫の費用の相場とは?倉庫選びのポイントを解説!|冷凍保管サービスコールドクロスネットワーク(COLD X NETWORK)
コメント